3D printing, also known as additive manufacturing, has revolutionized the way we create physical objects. It offers a wide range of processing methods, each with its own advantages and applications. In this article, we will explore the common 3D printing processing methods and their unique characteristics.
Fused Deposition Modeling (FDM)
Fused Deposition Modeling (FDM) is one of the most widely used 3D printing processes. In FDM, a thermoplastic filament is heated and then extruded through a nozzle onto a build platform. The material is deposited layer by layer to create the final object. FDM is known for its versatility, low cost, and relatively simple operation. It is commonly used for prototyping, rapid manufacturing, and producing functional parts.
Stereolithography (SLA)
Stereolithography (SLA) is an additive manufacturing process that uses a vat of liquid photopolymer resin and a UV laser to build parts layer by layer. The UV laser solidifies the liquid resin at the desired locations, creating a solid 3D structure. SLA is ideal for producing high-resolution, intricate parts with smooth surface finishes. It is often used in industries such as jewelry, dentistry, and aerospace for creating detailed prototypes and end-use parts.
Selective Laser Sintering (SLS)
Selective Laser Sintering (SLS) utilizes a high-powered laser to selectively sinter powdered material, typically nylon or other polymers, into a solid 3D structure. The process involves spreading a thin layer of powder over the build platform, then using the laser to fuse the particles together based on the 3D model’s cross-section. SLS is known for its ability to produce strong, durable parts with complex geometries, making it suitable for functional prototypes and low-volume manufacturing.
Direct Metal Laser Sintering (DMLS)
Direct Metal Laser Sintering (DMLS) is similar to SLS, but it uses metal powders instead of polymers. A high-powered laser fuses the metal powder together, layer by layer, to create fully dense metal parts. DMLS is valued for its capability to produce complex, high-strength metal components with excellent mechanical properties, making it ideal for aerospace, automotive, and medical applications.
Binder Jetting
Binder Jetting is a 3D printing process that uses a liquid binding agent to selectively bond powder particles together to form a solid object. This technique allows for the production of colorful, high-resolution parts and is commonly used in architectural models, artistic creations, and sand casting molds for metal parts.
Digital Light Processing (DLP)
Digital Light Processing (DLP) is similar to SLA but uses a digital light projector to cure the entire layer of resin at once, resulting in faster print times. DLP technology is known for its high printing speed and can produce detailed, accurate models with smooth surface finishes, making it suitable for a wide range of applications, including jewelry, dental, and consumer products.
Selective Laser Melting (SLM)
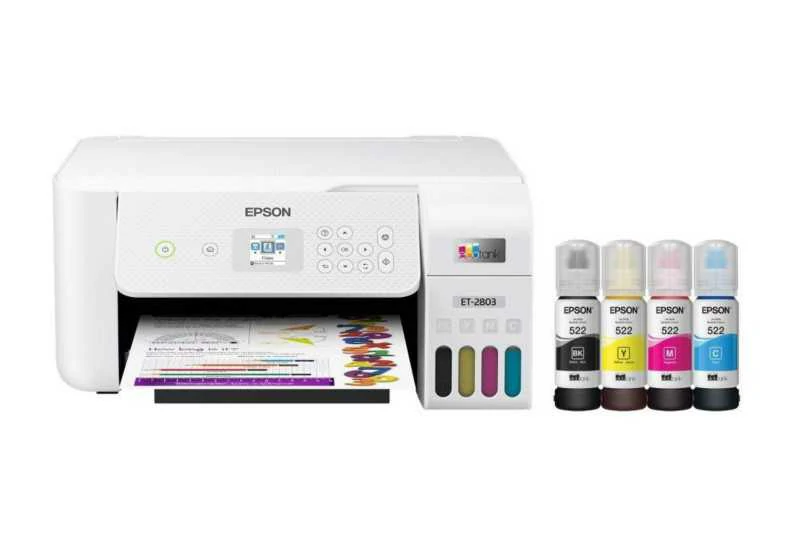
Selective Laser Melting (SLM) is an additive manufacturing technique that uses a high-powered laser to fully melt and fuse metallic powders, layer by layer, to produce dense metal parts. SLM is capable of producing parts with excellent mechanical properties and is commonly used in aerospace, medical, and automotive industries for manufacturing complex, high-performance metal components.
Electron Beam Melting (EBM)
Electron Beam Melting (EBM) is a similar process to SLM but uses an electron beam rather than a laser to melt and fuse metal powders. EBM is well-suited for producing large, complex, and highly durable metal parts, making it a preferred method for aerospace and medical applications.
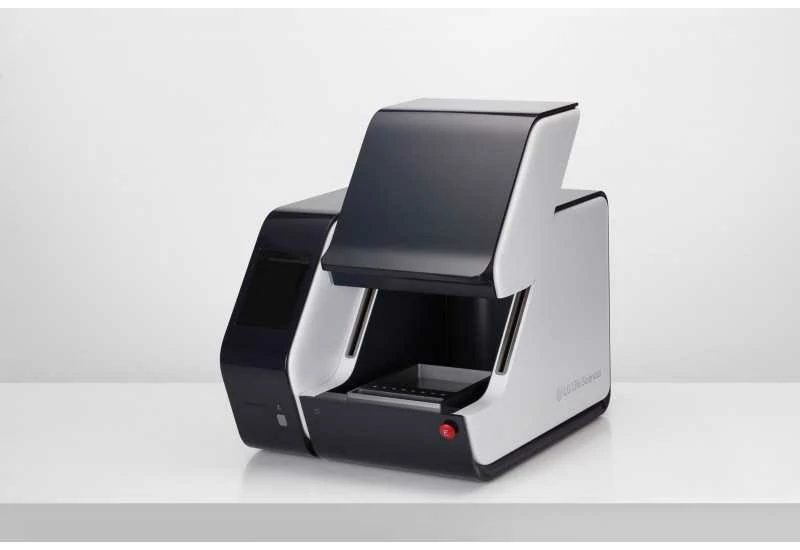
In conclusion, 3D printing offers a diverse range of processing methods, each with its own unique strengths and applications. From producing intricate prototypes with SLA to creating durable metal parts with SLM, the versatility of 3D printing technology continues to drive innovation across various industries. As the technology advances, we can expect to see even more sophisticated and efficient 3D printing processes emerge, further expanding the possibilities for additive manufacturing.