Selective laser sintering (SLS) is an additive manufacturing (AM) process in which a laser methodically sinters the particles of a polymer-based powder and builds parts layer by layer. Selective laser melting (SLM) is another form of AM but utilizes a metal powder (pure or alloy) instead. Despite these similarities, the three main differences between SLS vs. SLM are the material used to build the parts, the process used to build them, and the cost.
Since a metal powder is melted in SLM, the build process between the two machines is different. An inert gas (argon or nitrogen) must be pumped into the build chamber to facilitate melting. Consequently, high temperatures present within SLM systems necessitate sufficient cooling for parts before they are removed.
For both SLS and SLM, build times can be long. Also, the complexity of their technologies makes both processes relatively expensive. Regardless, one main advantage of SLS is that it can produce parts reflective of a plastic-injected part faster. SLM’s main advantage is that it can produce metal parts that otherwise would be non-machineable. Both systems can be excellent ways to expedite time-to-market via rapid prototyping and low-to-medium volume production.
In this article, we dive deeper into the differences and similarities of SLS vs. SLM to help provide a better understanding of which system is best for a project.
SLS Definition and Comparison to SLM
SLS was developed in the mid-1980s at the University of Texas at Austin with funding from the US Department of Defense. Patents for these AM processes have long expired, and many companies have developed lower-cost options for 3D-printer systems since.
SLS builds parts using a CO2 laser that selectively sinters and fuses thermoplastic polymer granules. When a layer is completed, the build platform descends and another layer of powder is deposited for sintering. This process repeats until the part is completed. Completed parts must cool, for up to 12 hours, before they are cleaned with compressed air or other blasting media. Compared to SLM, SLS can be considered an identical process except for thermoplastics rather than metals. The image below shows an SLS 3D printer:
A typical SLS 3D printer.
Image Credit: Shutterstock.com/Moreno Soppelsa
What Are the Advantages of SLS Compared to SLM?
The advantages of SLS compared to SLM are listed below:
- SLS-printed parts have excellent mechanical properties.
- SLS easily makes complex-geometry parts since no supports are needed.
- SLS allows the recycling and reusing of unsintered powders.
What Are the Disadvantages of SLS Compared to SLM?
The disadvantages of SLS compared to SLM are listed below:
- SLS printers have long lead times since only industrial-scale SLS printers are widely available.
- SLS parts commonly have poor and grainy surface finishes and may require post-processing to achieve desired surface finishes.
- Warping and oversintering can occur on large, flat surfaces and small holes in SLS-printed parts.
SLM Definition and Comparison to SLS
SLM was developed at the turn of the 21st century at the Fraunhofer Institute in Germany. The potential impact SLM has on the manufacturing industry is immense. An extensive range of possible metals can be used in SLM processes. SLM parts have properties equivalent to metal parts fabricated through traditional processes.
Like SLS, SLM builds parts using a high-powered laser and a powdered material. Unlike SLS, SLM systems melt powders to build parts and form compact, homogenous structures. Moreover, entire layers of a part are melted at once. When a layer has solidified, the build platform descends. Another layer of powdered metal is deposited for the process to repeat until the part is completed. The entire printing process occurs within a controlled environment; inert gases like argon or nitrogen are pumped into the system to facilitate melting. Completed parts must cool sufficiently before being removed from the printer.
SLM is near-identical to SLS. The only major difference is the material used: SLS creates plastic parts, and SLM creates metal parts. The image below shows a typical SLM 3D printer:
A typical SLM 3D printer.
Image Credit: Shutterstock.com/ID1974
What Are the Advantages of SLM Compared to SLS?
The advantages of SLM compared to SLS are listed below:
- An extensive range of potential materials makes SLM a well-rounded, robust alternative to traditional metal-fabrication methods.
- SLM can reduce manufacturing lead times and tooling costs.
What Are the Disadvantages of SLM Compared to SLS?
The disadvantages of SLM compared to SLS are listed below:
- SLM systems are expensive due to their costly technology and equipment.
- SLM requires extensive post-processing to achieve desired surface finishes.
- SLM requires increased material usage due to the need for support for overhangs on parts during printing.
Comparison Table Between SLS and SLM
A table of various attributes comparing SLS and SLM is shown below:
Uses thermoplastic powder
Yes
No
Uses metal powder
No
Yes
Inert gas needed
No
Yes
Extensive range of materials
No
Yes
Use for functional prototypes and small-to-medium-sized production
Yes
Yes
Extensive post-processing required
Yes
No
Need for supports
No
Yes
Complex geometries
Yes
Yes
Costly
Yes
Yes
Table. SLS vs. SLM Comparison
SLS and SLM are nearly-identical AM processes. They utilize similar technology, so are both expensive when compared to other AM processes. Both SLS and SLM produce parts that have equivalent properties to parts made through traditional methods such as injection molding or CNC machining. Therefore when picking between SLS and SLM, consider the final application of the part to be printed and whether plastic or metal would have better performance.
SLS vs. SLM: Technology Comparison
Technology refers to the equipment and tools used to produce a part. Both SLS and SLM systems have similar complex technologies and processes. They use high-powered lasers, thermoplastic or metal powders, and specialized 3D-printing environments. The primary differences between the two forms of AM as it relates to technology are the addition of gas and the need for a special printing environment for SLM processes.
SLS vs. SLM: Material Comparison
SLS prints parts from thermoplastic powders such as Nylon 11, Nylon 12, and its derivatives. SLM prints parts from pure metal or alloys. While nylons are predominantly used in SLS, the possible materials that can be used with SLM are much more extensive.
SLS vs. SLM: Product Applications Comparison
Possible product applications of SLS vs. SLM depend on whether a thermoplastic or metal part would be more ideal. While both AM methods can provide parts that are environmentally stable, deciding between the two ultimately comes down to two factors: load bearing and weight. SLM may be the better option if higher loads are exerted on the parts. If light weight is more critical, SLS may be better.
SLS vs. SLM: Print Volume Comparison
The print volumes for SLS and SLM are similar since the two AM methods are nearly identical. SLS printers can have print volumes up to 550 x 550 x 750 mm while SLM printers can have volumes up to 350 x 350 x 350 mm. There isn’t a substantial difference in print volume between the two.
SLS vs. SLM: Surface Finish Comparison
SLS printers produce parts with excellent surface finishes, but sometimes leave surfaces feeling grainy and powdery. Surfaces can be post-processed with blasting media such as: water jet or sand, spray painting, or lacquering. SLM printers can produce metal parts with exceptional surface finishes that seldom require post-processing. SLM parts can be post-processed to increase corrosion resistance.
SLS vs. SLM: Cost Comparison
Because both SLS and SLM systems use complex, advanced technologies, they can be expensive. SLS systems start as low as $18,000 and can go as high as $100,000. SLM printers are more costly. They range from $55,000 to $350,000.
What Are the Mutual Alternatives to SLS and SLM?
There are no mutual alternatives to both SLS and SLM printing methods. This is because one produces thermoplastic parts and another produces metal parts. However, for each case, alternative processes do exist.
What Are the Similarities Between SLS and SLM?
Similarities between SLS and SLM include:
- Both SLS and SLM use a laser and a powdered material to produce parts.
- Both SLS and SLM are excellent for prototyping and proof-of-concept.
- Both SLS and SLM can rapidly produce parts for low-volume production.
- Both SLS and SLM can produce parts with complex geometries.
What Are the Other Comparisons for SLS Besides SLM?
Besides FDM, other comparisons for SLS include:
- SLS vs. MJF: Multi Jet Fusion (MJF) is comparable to SLS because both methods use a powder and a fusing mechanism to build parts. There are two main differences between SLS vs. MJF, however. The MJF process uses ink agents and infrared frequencies to solidify parts. It can also print much faster than SLS since entire layers are heated at once, rather than particular areas of the build platform in SLS. For more information, see our article on SLS vs. MJF.
- SLS vs. SLA: SLA is a comparative alternative because it can be used for both functional prototypes and production. The difference between SLS vs. SLA is that SLA has an even greater resolution than SLS. It offers the highest resolution out of any form of AM and therefore can also be used for molds, tooling, patterns, and textures. For more information, see our article on SLS vs. SLA.
What Are the Other Comparisons to SLM Besides SLS?
Other comparisons to SLM besides SLS include:
- SLM vs. DMLS: Direct metal laser sintering (DMLS) is comparable to SLM because both methods utilize a metal powder to produce parts. The main difference between SLM vs. DMLS is that in DMLS, metal powders are sintered, rather than melted – similar to SLS processes for thermoplastics. DMLS printers cannot achieve the same level of resolution as SLM since metal powders are not melted and homogenized into the structure. For more information, see our article on DMLS vs. SLM.
- SLM vs. EBM: Electron beam melting (EBM) is another comparison to SLM. The difference between SLM vs. EBM is that rather than using a laser to melt powders in SLM, an electron beam is used in EBM. EBM produces parts that are of similar resolution to SLM equivalents. However, only a select few metals, like titanium alloys, can be used.
Summary
This article summarized the differences between SLS and SLM 3D printing technologies.
To learn more about SLS vs. SLM and to help select the perfect technology for your products, contact a Xometry representative.
Xometry offers a full range of 3D printing services for your project needs. Visit our Instant Quote Engine to get a free, no-obligation quote in minutes.
Disclaimer
The content appearing on this webpage is for informational purposes only. Xometry makes no representation or warranty of any kind, be it expressed or implied, as to the accuracy, completeness, or validity of the information. Any performance parameters, geometric tolerances, specific design features, quality and types of materials, or processes should not be inferred to represent what will be delivered by third-party suppliers or manufacturers through Xometry’s network. Buyers seeking quotes for parts are responsible for defining the specific requirements for those parts. Please refer to our terms and conditions for more information.
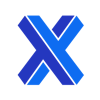
.webp)