SLS (selective laser sintering) is a 3D printing technique that uses a laser to fuse together small particles of plastic, metal, glass, or ceramic powder into a solid object. SLA (stereolithography) uses an ultraviolet (UV) laser to cure (harden) photosensitive resin into the desired shape. Both technologies employ a laser as part of their build process, but they differ in terms of build speed, precision, price, and processing. A full understanding of the choice between SLS vs. SLA requires more background information.
A major advantage SLS has over SLA is in the time it takes to manufacture a part. It has a shorter lead time. Therefore, more such parts can be produced per day. However, if precision details are important, SLS becomes the best choice because it produces parts with tighter tolerances.
In this article, we will compare and contrast these two types of 3D printers. We will also take a cursory look at other alternatives that can serve as replacements for either one of them.
SLS Definition and Comparison to SLA
SLS was created in the 1980s at the University of Texas in Austin by Dr. Carl Deckard and Dr. Joe Beaman. SLS is a 3D printing technology that uses a powerful laser to selectively fuse layers of powdered particles. Most such machines use nylon-based or polymer-based build materials, though more advanced versions have been created to fuse materials with higher melting temperatures.
Each print begins with a digital version of the part, built into a computer. The SLS machine turns that into a physical object by tracing out the geometry of each successive 2D slice of the object, fusing powder at the necessary points. After one layer is finished, another fine layer of powder is applied and the process repeats. SLS produces parts with good mechanical properties making them suitable for end-users. This is not the case for SLA, the products of which are not as tough as those of SLS. The image below shows how an SLS printer works:
To learn more, see our article on What is SLS.
How an SLS printer works.
Image Credit: Shutterstock.com/MarinaGrigorivna
What Are the Advantages of SLS Compared to SLA?
There are advantages to using SLS vs. SLA. Some are listed below:
- SLS parts need no support structures during production while SLA parts do. The surrounding powder serves to support overhanging components during the building process. SLA parts need to be designed with supporting structures or built in such a way that makes the parts self-supporting.
- The SLS production process is faster than SLA. That makes it handy for rapid prototyping activities.
- The parts produced via SLS are tougher than those of SLA, so they’re more often used as functional parts.
What Are the Disadvantages of SLS Compared to SLA?
Though SLS is very capable, it still has its disadvantages. These include:
- SLS machines are more expensive than SLA machines.
- The SLS laser demands a lot of electricity. This means the print needs to be completely enclosed and shielded. The laser beam in SLA uses less power; users can view the print while it is enclosed behind plastic or tinted glass.
- SLS machines are bulkier. They typically fill an entire laboratory workbench. In contrast, SLA machines are often designed as desktop devices.
SLA Definition and Comparison to SLS
Chuck Hull, the founder of 3D Systems, invented the SLA process and coined its name in 1986. In 1992, an upgraded version was produced that made the fabrication of complex parts possible — and it did so quicker than old machines as well. Among 3D printing technologies, SLA is the oldest.
SLA is an additive manufacturing process that uses an ultraviolet (UV) laser to cure a photopolymer or a light-sensitive resin. It builds parts upside-down, with the build plate in contact with the reservoir of resin. The laser is directed at specific points on the plate until the desired sections solidify. The plate then raises up out of the reservoir so the next layer can be cured, fusing with the previous layer of hardened resin. The part appears to rise out of the liquid pool. Critically, and unlike SLS, SLA can print to extremely tight tolerances. The image below shows how an SLA 3D printer works:
To learn more, see our guide on What is SLA.
How an SLA 3D printer works.
Image Credit: Shutterstock.com/ZoranOrcik
What Are the Advantages of SLA Compared to SLS?
SLA’s advantages compared to SLS are:
- SLA systems provide greater resolution than their SLS counterparts.
- SLA produces parts with better surface finishes than SLS. Its parts are comparable to injection-molded parts.
- SLA machines are less bulky than SLS. For this reason, they can serve as desktop devices.
What Are the Disadvantages of SLA Compared to SLS?
Listed below are the disadvantages of SLS compared to SLS:
- SLA cannot print parts as large as those of SLS.
- The resin in SLA is not environmentally friendly. The resins produce unpleasant fumes and require one to wear gloves when handling them. On the other hand, SLS uses polymer powder such as nylon which is not particularly harmful except to people with specific allergies.
- SLA produces weaker parts compared to SLS. They are best used as proofs of concept or for experimental use.
Comparison of SLS and SLA
The table below highlights some key attributes when comparing SLS vs. SLA:
Sensitive to UV light
No
Yes
Rough surface finishes
Yes
No
Limited materials
Yes
No
Needs no supporting structures
Yes
No
Fast production process
Yes
No
Expensive machine
Yes
No
Parts produced are only for experimental use
No
Yes
Table. SLS vs. SLA Comparison
The polymer resin used in SLA is sensitive to UV light. As such, it should be kept away from sunlight or any other source of light that contains UV radiation. SLS products do not have this shortcoming, and nor do they need supporting structures during manufacturing. The unfused powder particles are sufficient to provide support.
SLS vs. SLA: Technology Comparison
The high-powered laser in SLS is completely enclosed, giving operators no view of the print. SLA laser output is significantly lower in power and requires only tinted glass or a plastic enclosure to prevent the UV light from escaping.
SLS vs. SLA: Material Comparison
The polymer powder in SLS is easy to handle but users must wear gloves while handling SLA parts. The resin used in the production process is slightly harmful. Some commercially available production materials used in SLS include: polyaryletherketones, thermoplastic elastomers, polystyrenes, and nylon. SLA materials include but are not limited to: epoxy photopolymer, acrylic photopolymer, and some others with polypropylene-like and ABS-like properties.
SLS vs. SLA: Product Applications Comparison
SLS produces parts that are tougher than those of SLA. This makes them better options for mechanical or end-use applications.
SLS vs. SLA: Print Volume Comparison
Thanks to its size and the sintering time, SLS prints faster than SLA both on large- and small-scale models. In addition to this, SLS requires no supporting structures during the building process.
SLS vs. SLA: Cost Comparison
SLS devices are generally more expensive than SLA devices. In both cases, the cost is compounded over time since materials such as resin or powder have to be purchased regularly. SLS machines can be purchased for as little as $10,000 or as much as $650,000. The cost depends on the maximum build volume, minimum layer thickness, print speed, laser type, and the build materials it can accept. SLA machines, on the other hand, usually fall in the range of $3,750 to $5,000, depending on the size. They can be classified into four different types: DIY, advanced hobbyist, professional and performance, and business and industrial.
What Are the Mutual Alternatives to the SLS and SLA?
A mutual alternative to SLS and SLA is:
- MJF: MJF (Multi-Jet Fusion) bears some similarities to both SLS and SLA. It can be used to produce end-use parts like its SLS counterpart. But like SLA, it does not require a high-powered laser and is a good option for functional prototypes or proofs of concept.
What Are the Similarities Between SLS and SLA?
SLS and SLA share some basic similarities:
- Both technologies employ lasers to fuse material.
- Both require post-processing. SLS parts have to be cleaned to remove excess powder and may need extra work to match surface-quality specifications. Similarly, SLA parts have to be cleaned to get rid of uncured resin.
What Are the Other Comparisons for SLS Besides SLA?
Listed below are the 3D printing technologies that can also be compared to SLS:
- SLS vs. SLM: SLM (selective laser melting) is a similar powder-bed technique but fuses metallic powder rather than polymers. For more information, see our article on SLS vs. SLM.
- SLS vs. EBM: EBM (electron beam melting) is similar to SLM in that it melts and prints metal parts. However, it is done under a vacuum and uses an electron beam rather than a laser. It can achieve higher temperatures, resulting in better melting and a stronger bond between particles. For more information, see our article on EBM vs. SLS.
- SLS vs. FDM: In SLS, the polymer powder is heated to a temperature below the melting point before a high-power laser is applied to specific spots to actually melt it. FDM, or fused deposition modeling, utilizes a heated nozzle to melt and extrude layers of filament material. The resulting liquid is fused to previous layers to create the required shape. Both designs require heat before fusion takes place. For more information, see our article on SLS vs. FDM.
What Are the Other Comparisons for SLA Besides SLS?
Listed below are the 3D printing technologies that can also be compared to SLA:
- SLA vs. MJ: MJ (material jetting) machines feature an inkjet-like print head that sprays liquid photopolymer in the pattern of a part’s cross-section. That spray is then followed by a UV light that cures the polymer.
- SLA vs. DLP: Like SLA, DLP (digital light processing) printers subject select portions of photopolymer resin to ultraviolet light in order to cure them. While SLA uses a laser beam to selectively cure the resin, DLP utilizes a projector light and thousands of microscopic mirrors to direct it to or away from the build surface. For more information, see our article on SLA vs. DLP.
Summary
This article summarized the differences between SLS and SLA 3D printing technologies.
To learn more about SLS vs. SLA and to help select the perfect technology for your products, contact a Xometry representative.
Xometry offers a full range of 3D printing services for your project needs. Visit our Instant Quote Engine to get a free, no-obligation quote in minutes.
Disclaimer
The content appearing on this webpage is for informational purposes only. Xometry makes no representation or warranty of any kind, be it expressed or implied, as to the accuracy, completeness, or validity of the information. Any performance parameters, geometric tolerances, specific design features, quality and types of materials, or processes should not be inferred to represent what will be delivered by third-party suppliers or manufacturers through Xometry’s network. Buyers seeking quotes for parts are responsible for defining the specific requirements for those parts. Please refer to our terms and conditions for more information.
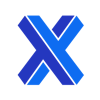
.webp)